Overview
Tasked with managing the South Island’s largest port, Lyttelton Port Company facilitates the import and export of over $10 billion of goods annually. The company’s 600 staff manage nearly half the island’s container volume – around 430,000 TEUs of container cargo every year.
Traditionally LPC had utilised decidedly manual means to manage the vast amount of cargo that passed through its port. Logistics Officers worked out of a facility that relied on traditional ‘line of sight’ practices – human eyes, enhanced by a set of old-fashioned binoculars, would register cargo information, logging it in the appropriate system.
As the amount of cargo increased exponentially, LPC concluded that their traditional practices were far from sustainable. Soon an opportunity to evolve presented itself – the construction of a new LPC headquarters.
“Right at the start of the wider project to relocate our terminal operations into LPC’s new building, the setup of the control room was identified as a critical risk to the project,” explains Joe Smedley, Head of Container Operations, LPC. “All terminal activity was controlled through the control room, where staff looked through glass windows that granted them an almost unrestricted view of terminal operations.”
The plan was to transplant the control room to a location where it would have little to no direct view of terminal operations, relying instead on technology to deliver visuals.
Having previously worked together, LPC decided to get in touch with our team at Millpond.
Approach
The new Operations Control Room would rely not on human eyes, but on CCTV technology. This solution needed to win the confidence of Logistics Officers, proving that it could be used to manage container movements safely and efficiently, and without any degradation in performance when compared to traditional line of sight methods.
The challenges of the project were many and varied. The solution had to be designed, installed and tested while the physical control room was under construction, and without causing any form of interruption to container operations.
All Logistics Officers needed to be trained in a one-on-one capacity, to address their concerns regarding:
- Their ability to use the technology unaided
- The reliability ad robustness of the technology
- The ability of the technology to match the efficacy of line of sight methods
- Whether the ergonomics of the room were suitable for working through long shifts.
Millpond’s solution, managed in concert with seven different vendors, included:
- 22 digital, networked cameras
- 22 communications cabinets
- New underground fibre cabling and network switches
- Video recording and viewing software & servers
- An ergonomically designed control room, featuring a multi-functional video wall with six 46″ monitors
The system was successfully tested the week before Christmas in 2017, and the final ‘go live’ was achieved in one overnight shift in January 2018.
Results
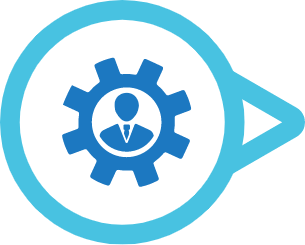
Millpond managed seven different vendors as part of the engagement.
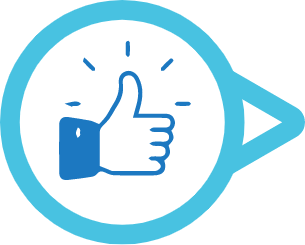
Millpond facilitated a full scope and budget for input into the Business Case, which was approved.
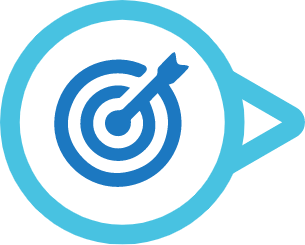
The project met all functional and change management requirements goals, within the project budget.
Summary
Despite the project’s complexity and the minimal room for error, Millpond and LPC were successful. There was no interruption to service during the entire process, and staff transitioned with no additional help. The project was delivered on time and well within budget.
According to Smedley, the reasons for Millpond’s success were many and varied.
“It began with a well thought out and executed training plan. We had weekly coordination meetings between all vendors so that all parties understood key dependencies and dates. An engaged Steering Committee helped to quickly clear any issues that were escalated to them. We were able to identify a raft of cost savings during the life of the project, granting us greater financial flexibility. Finally, focus was a key factor – we had a PM who could focus the majority of his time on the one project.”
The result? LPC’s Logistics Officers now have a superior view of container operations, as cameras can be panned and zoomed to give views from a wide variety of angles and distances. And after decades of dedicated service, the binoculars have been gifted their richly deserved retirement.